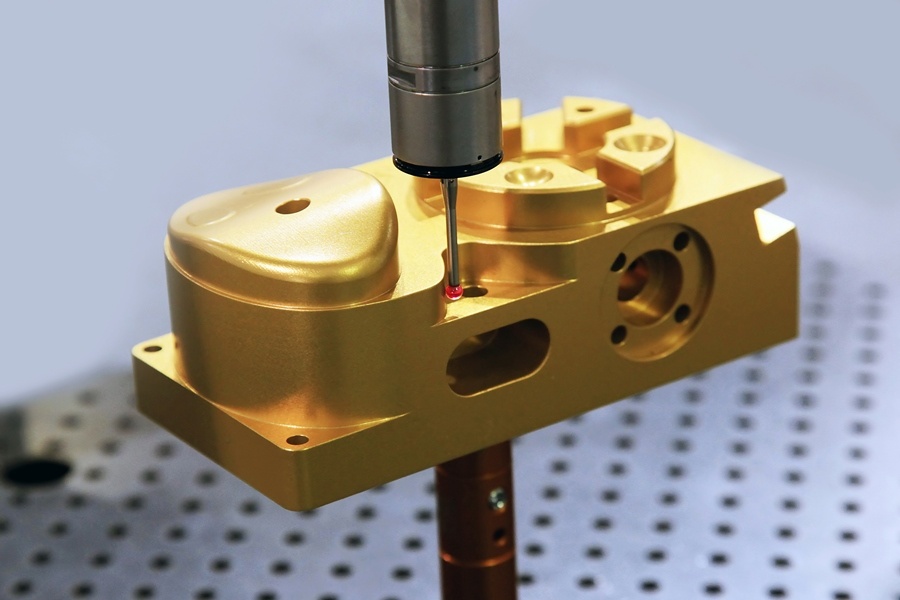
One of the most commonly used metals for various applications across a range of industries is brass.
Providing manufacturers with a dark gold colouring and shiny appearance, brass is a great choice for applications ranging from decorative items to plumbing parts, household appliances, electrical equipment, and various types of machinery.
Brass is not only practical and decorative; it is also incredibly versatile. A blend of varying levels of zinc and copper, the material brass can produce different mechanical and chemical properties, which steel metalworks use to benefit all applications.
Sheet metal fabrication involves a series of varied processes, one of which is laser cutting and engraving.
Laser cutting is a process suitable for brass; however, brass is a reflective material, making laser cutting challenging for those with little to no experience.
In this post, we look at laser-cutting brass sheets and why working with a professional fabrication team is the best way to ensure a high-quality finished product.
What is brass laser cutting?
Brass laser cutting involves using laser technology where a laser beam is emitted from the equipment using energy to heat the brass and provide the cut.
A gas is then used alongside the laser to blow out and remove the laser-cut metal, providing a clean and precise cut.
Brass laser cutting has no cutting force to the brass, so there is no deformation of the material, allowing a professional sheet metal contractor the ability to achieve precise processing without any burrs, as well as the ability to handle large sheet sizes and varying thickness levels.
Fibre lasers tend to be used over C02 lasers as they can avoid the high reflectivity of the brass, allowing for a clearer cut. Fibre lasers also offer a higher power output and a shorter wavelength (meaning less reflectivity), which is required for brass to avoid burrs from occurring.
Fibre lasers can also melt brass quicker due to their greater energy output, and brass must be in a molten state for a clean cut.
Fibre laser cutting cuts quickly and precisely, with the cutting slit narrow and smooth. This laser technology can also handle a variety of complex patterns, making it suitable for various design applications and specifications.
(Check out one of our other posts on `what is aluminium laser cutting` to find out more about the various materials and fabrication processes required to achieve a quality cut outcome.)
Brass engraving is also popular, as we see it used on brass plates and trophy engravings. Brass engraving is the process of removing the upper surface of the brass material only, to create distinct patterns and etchings.
Laser-cutting brass sheet
Brass is a non-ferrous metal alloy that offers good abrasion resistance and a shiny surface.
However, cutting brass requires a high level of efficiency and precision, and you must be aware that:
Brass is highly reflective of infrared light, and if not managed or handled appropriately, it can reflect the laser beam, causing problems for the laser optics and even the person managing the equipment.
The laser energy used to cut brass is not absorbed well, as most of the laser is reflected. This makes laser cutting brass extremely challenging and a process that should only be carried out by experienced sheet metal fabricators.
The brass must be molten to lower its reflectivity and enable the cut. The more you can lower the reflectivity, the more you can improve the laser energy absorption, which leads to a cleaner cut.
Using laser for brass cutting
For a successful brass cut:
Use the correct power setting – this should typically be set high, i.e., the maximum the machine can provide, as this reduces the time for the brass to become molten, reducing the time the brass is at its highest reflectivity. Ultimately, the higher the laser power, the faster the cut.
Opt for the right cutting speed – this is often set at a low speed; we recommend 10 to 15% less than the machine’s maximum. The slower speed makes brass cutting much easier.
Position the point of focus as close to the top of the brass sheet as possible without affecting the material’s quality.
Choose the right cutting gas—for brass, nitrogen is the best choice, as this gas can mechanically remove the cut metal, once it is in its molten state effectively. Nitrogen also helps prevent the metal from forming back again after the laser has passed through.
Material size—You need to be aware of the material size you’re working with, as you will need to use the right tools and equipment, such as a machine with the right bed size to accommodate the sheet metal in question.
Sheet metal fabricators
Offering you precision, speed, efficiency, and a cost-effective brass cutting solution, the team at Morfabrication are experts in the field of laser cutting sheet metal.
We work with your design specifications and can handle even the most intricate and complex cuts.
Providing you with a finished project that is clean, has smooth edges, minimal burring, and a production process that causes minimal waste.
If you have a project coming up that requires precision fabrication, contact the team at Morfabrication today to see how we can help.